But the home-grown firm saw an opportunity to grow its business three years ago during a corporate visioning exercise, when its management reflected on the amount of waste it was sending straight to the incinerator.
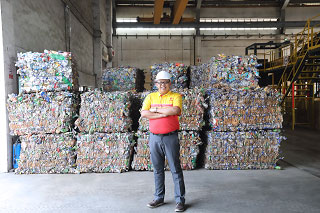
“We realised that quite a fair bit of things can be recovered from the waste itself. Instead of spending money to burn it, we thought why not try to recover the resources from the waste,” says Mr Lim Jo Hann, Senior Vice President of Operations.
This marked the beginning of the company’s material recovery facility at Sungei Kadut that started operations in end 2018. It features a semi-automatic sorting system that separates paper, leaves, plastics and glass bottles using a ballistic separator system. Another electromagnetic system sorts out non-ferrous metals.
Some of the output from the sorting system such as plastic bottles, aluminum cans and carton boxes are sent to traders to be exported overseas, while other materials such as leaves and sand are sold to farms to create compost. The remaining waste is then sent to the incinerator to be disposed.
Prior to introducing the system, CTM tried to use manual ways to pick out recoverable resources such as the leaves. However, this was time and manpower intensive, and resulted in the recovered resources being not clean enough for farms to use as compost.
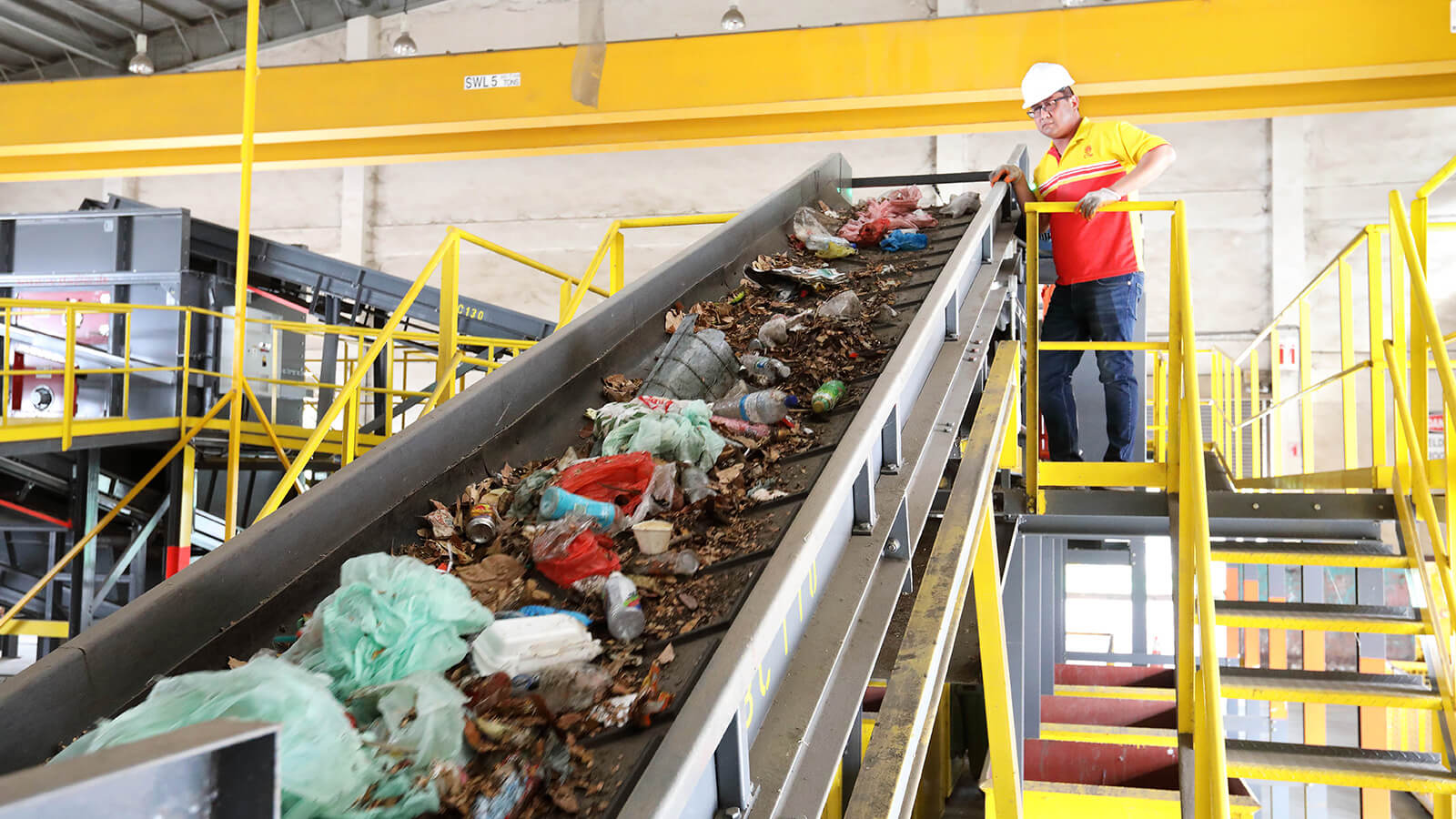
Mr Lim acknowledges that many companies still incinerate waste because it is cheaper than investing in technology for a sorting system. CTM’s waste recovery facility alone amounted to S$1.6 million. But, the benefits of this investment are multifold, he shares.
“The facility makes the separation process easier so workers don’t have to bend down and shovel. They can just stand at their workstations and pick out useful items,” he explains.
More importantly, the system makes waste disposal more environmentally sustainable while creating cost savings for the company and a new revenue stream from the sale of recovered materials.
Instead of incinerating all 800 tonnes of waste collected every month, they now recover 300 tonnes of leaves, timber, plastic, paper and metal cans, amounting to a recovery rate of close to 40%.
This has in turn saved the company 20% on incineration costs each month. CTM’s annual turnover also increased by 10% in 2018, after the introduction of its material recovery facility and with growth in other areas, shares Mr Lim.
Additionally, CTM can now offer clients a full package of cleaning, waste management and recovery services, which clients find attractive. This is especially so for companies that focus on environmental sustainability, he adds. The company now handles both cleaning and waste management for Changi Airport’s newest addition, Jewel.
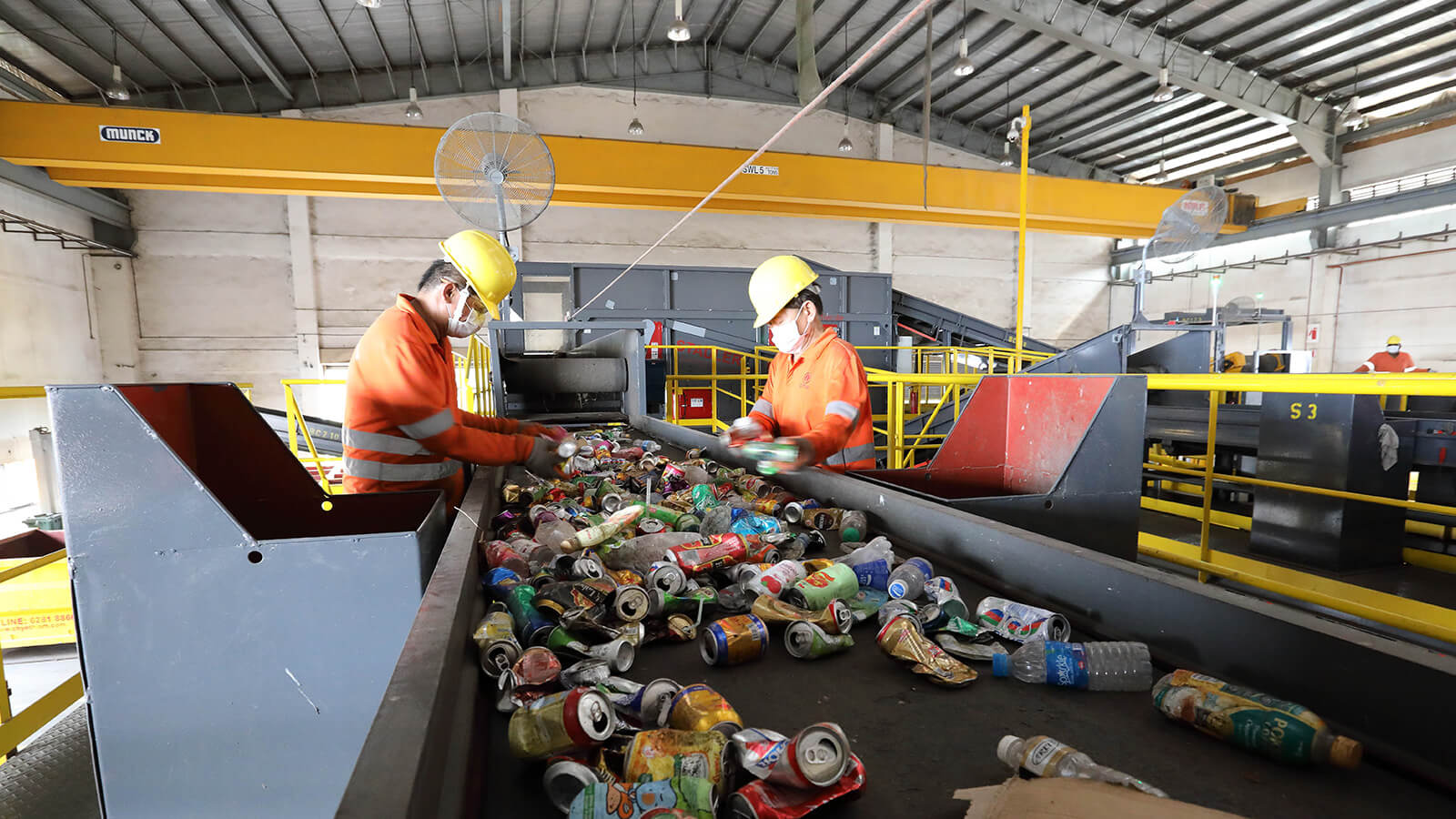
To make the material recovery facility a reality, Mr Lim and his team had their work cut out for them. They customised and put together the entire system from scratch so it could deal with the specific types of waste the company handles. They first visited overseas vendors to view and compare the different machines, and engaged a consultant for system integration, before purchasing the parts from different vendors and assembling the system in-house.
At the same time, the management ensured that staff received training to use the new system. Concurrently, to prepare staff for the overall future direction of the company, they also held town hall sessions and teambuilding exercises. All these efforts made it easier for employees to buy into the idea, says Mr Lim.
Other innovative green initiatives by the company include the adoption of ionized water as a disinfectant for cleaning. This move has allowed the company to not just reduce the use of harmful chemicals but also prolong cleaning cycles. This saves resources and boosts productivity – benefits that CTM’s clients appreciate as well.
In the future, the company plans to continue innovating and tapping technology, to do their part for the environment while staying competitive.
Says Mr Lim, “The problem statement for Singapore is that Semakau landfill is running out of space. With the government’s push towards zero waste, it’s a good business opportunity for us and a chance to do our part.”