JTC Space @ Tuas is a sight to behold. Completed in 2017, the integrated development sits on 6.2 hectares of land and towers impressively over its neighbours. As trains pull in and out of the nearby Gul Circle MRT station, commuters are treated to sights of the building’s exterior, which whizz by in a vivid blend of blue, grey, and green.

The first of its kind, JTC Space @ Tuas caters to multinational corporations (MNCs) and small and medium enterprises (SMEs) from a diverse range of industries such as oil and gas, precision engineering, and general manufacturing. Thanks to its creative design, JTC Space @ Tuas fits seven land-based factories, 36 ramp-up factories, 95 flatted factories, a multi-storey heavy vehicle carpark, plus a workers’ dormitory with recreational facilities and an amenity centre, in its footprint.
“With JTC Space @ Tuas, we wanted to maximise land use and provide a seamlessly integrated environment where collaborations can easily take place,” shares Bij Borja, the architect involved in the construction of JTC Space @ Tuas. “Housing different typologies within a single development really pushed the boundaries when it came to land intensification.”

For senior principal project manager Paul Tan, working on the mammoth project presented several firsts for him, including the use of Prefabricated Pre-finished Volumetric Construction (PPVC), which was an emerging method of construction then. He recalls: “It was difficult for us to find contractors and industry players familiar with PPVC at that time since the construction technology was so new.”
Here, the duo shares their experience working on JTC Space @ Tuas:
What makes JTC Space @ Tuas unique?
Tan: JTC Space @ Tuas was conceptualised as an integrated “hub”, co-locating landed and flatted factories, amenity provisions as well as dormitory and heavy vehicle parking spaces all in one development. The intention was to optimise and intensify land, while reducing transportation costs and the daily traffic congestion due to the ferrying of workers and goods. The sheer size of the project (6.2 hectares, or around nine soccer fields) also made it quite daunting, as we were embarking on such a massive project.
Borja: This was also the first time we used PPVC. Modules are manufactured off-site and then installed on-site like piecing together Lego blocks. This resulted in significant time and manpower savings as compared to conventional cast-in-situ concrete construction.
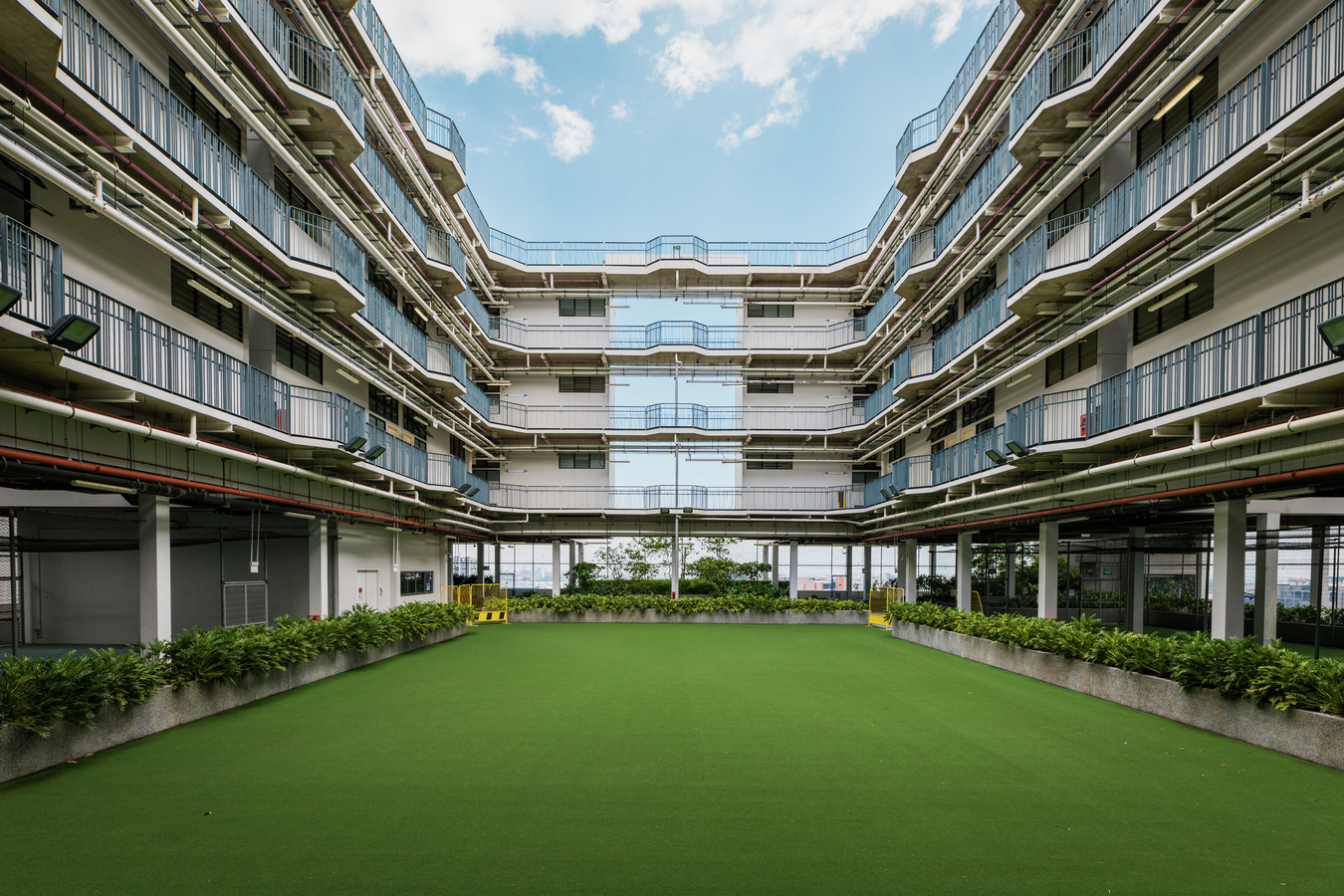
What were some challenges you faced?
Tan: JTC Space @ Tuas was the first time we brought different typologies together under one roof. As such, there were many complexities. Each typology had its own set of stringent set of compliances/requirements, so there were many different guidelines to adhere to. We had to engage all relevant authorities early so that they had ample time to carry out their internal discussions.
On top of that, it was challenging to find contractors, suppliers, and industry players familiar with PPVC at that time, since the technology was so new. When we were evaluating the construction tender, we looked out for contractors with vertically integrated businesses /experiences to handle pre-cast components and transport and heavy lifting subsidiaries. Local contractor, Tiong Seng Contractors fit the bill, having supplied the Housing and Development Board (HDB) with pre-cast bathroom units (PBUs). Our aim was also to help our construction industry upskill as we felt that developing expertise in this new method would greatly help them in their future projects.
We were very fortunate to have like-minded contractors and suppliers. We were all very excited about using this new PPVC technology. Kudos to Tiong Seng — they were more like a partner on this journey rather than a contractor as they pro-actively suggested fresh ideas and insights.
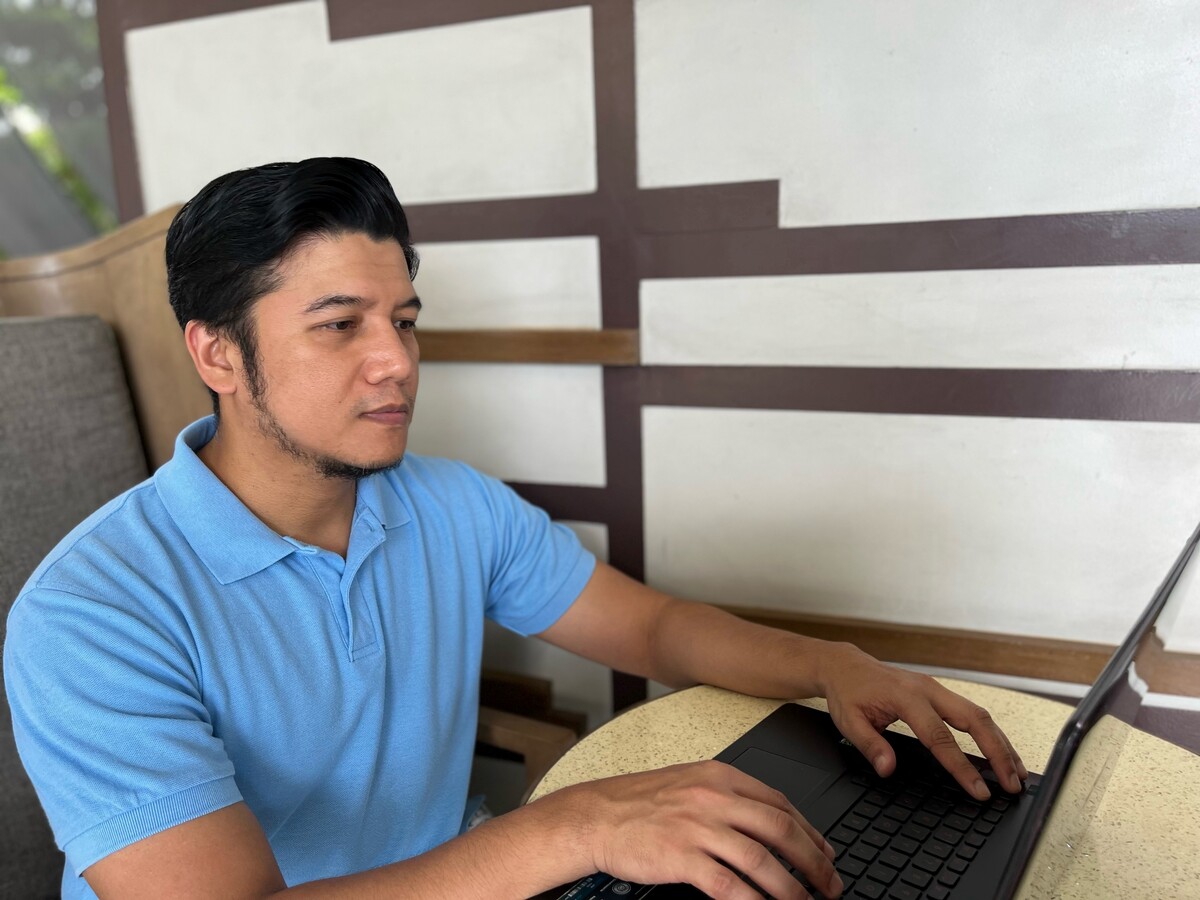
What were some memorable moments from this project?
Tan: The most memorable moment for me was Senior Minister Teo Chee Hean’s visit to Space @ Tuas when it was still in its construction phase. SM Teo and his entourage, which included representatives from other government agencies, had expressed excitement to find out and learn more about PPVC technology.
In addition, we also hosted the Hong Kong Housing Authorities during a learning trip to see if PPVC could be a possible solution to ramp up the supply to Hong Kong.
I was happy to see that the team efforts paid off and we were also recognised for our PPVC skills as well as our ability to take on complex projects. Soon after the visit JTC, was appointed as a Centre of Excellence for Building and Infrastructure in 2016.
Another memorable aspect of the project was the level of pre-casting involved – I can still remember the numbers! There were 1,700 pre-cast columns, of which the heaviest weighed 50 tonnes. There was also 4km of internal drains network and we overcame the challenge with some out of the box proposal by Tiong Seng, 288 PPVC modules for three storeys of dormitory.
Borja: The groundbreaking ceremony of JTC Space @ Tuas back in 2015 was particularly memorable as it signaled that all our plans were going to become a reality. The ceremony was also a testimony of JTC’s commitment in developing innovative infrastructure to support the growth of the manufacturing industry.
What were some lessons gleaned from working on this project?
Tan: While authorities were most concerned about the fire integrity of PPVC at that time, they now have more confidence in this technology. JTC Space @ Tuas had three storeys of dormitory spaces, but these days, developers are going up to 30, 40 storeys with PPVC. This really shows how this technology has come a long way in such a short span of time.
Of course, this increased confidence and credibility would not have been possible without inspection regimes. Since PPVC components are fabricated off-site, factory and site inspections are paramount to ensure compliance to approved drawings and code.
Borja: For me, the close coordination of all disciplines is crucial, especially for large scale projects as the different elements of the building are all interrelated. It is also important to fully understand the operations and technical requirements of the industry the development is catering to, so that we can better design the buildings and spaces to suit their needs.

Any advice you would like to share with fellow or new project managers?
Tan: Don’t be afraid to try new things. You don’t really get chances often, so to be a part of an exciting project that pioneers new technology is always something worth looking forward to and to be embraced rather than avoided.
When working on a project for over a long period, you develop a sense of affinity and ownership. Whenever I’m at JTC Space @ Tuas, I still remember the satisfaction and joy derived from seeing the building to near completion. I’m proud of this project notwithstanding its “pimples” and all.