Drive along Seletar Aerospace Park (SAP) and you’ll notice a new addition to the aerospace hub: the recently completed JTC aeroSpace Phase 3 (AS3). Situated in proximity to the facilities of big-name industry players such as Airbus, GE Aviation, and Rolls Royce, the cluster of nine buildings provides plug-and-play solutions to help aerospace companies set up their operations efficiently, and with a lower upfront capital investment.
From drafting the first blueprints to laying the first foundation, getting the project off the ground was no walk in the park. As the site sits in the direct flight path of the Seletar Airport runway, the development was subjected to height constraints, says Shaun Tan, the deputy director of JTC’s Urban Design & Architecture Division and the architectural Qualified Person (QP) involved in the project. Sophie Zheng, the second architect who lent her expertise to AS3, adds: “The team had to coordinate closely with the Seletar Airport control tower throughout the design and construction stages.”
For principal project manager Jeck Sees Teo, COVID-19 also threw a spanner in the works. “You can plan for contingencies and hope they never happen,” she recalls. “The pandemic affected the progress of the construction.” Here, the project team shares more about the development and what went into bringing the project to fruition.
What makes AS3 unique?
Teo: AS3 is the third phase of the standard factories development in Seletar Aerospace Park, following two earlier successful phases. Close to 100% of this project was done in-house. The planning and design leveraged on JTC’s capabilities, with a full internal project team and Qualified Persons (QPs) taking on the design and project management roles. AS3 presented a great opportunity for JTC to build our in-house capabilities, which will allow us to take on greater and more complex projects in the future.
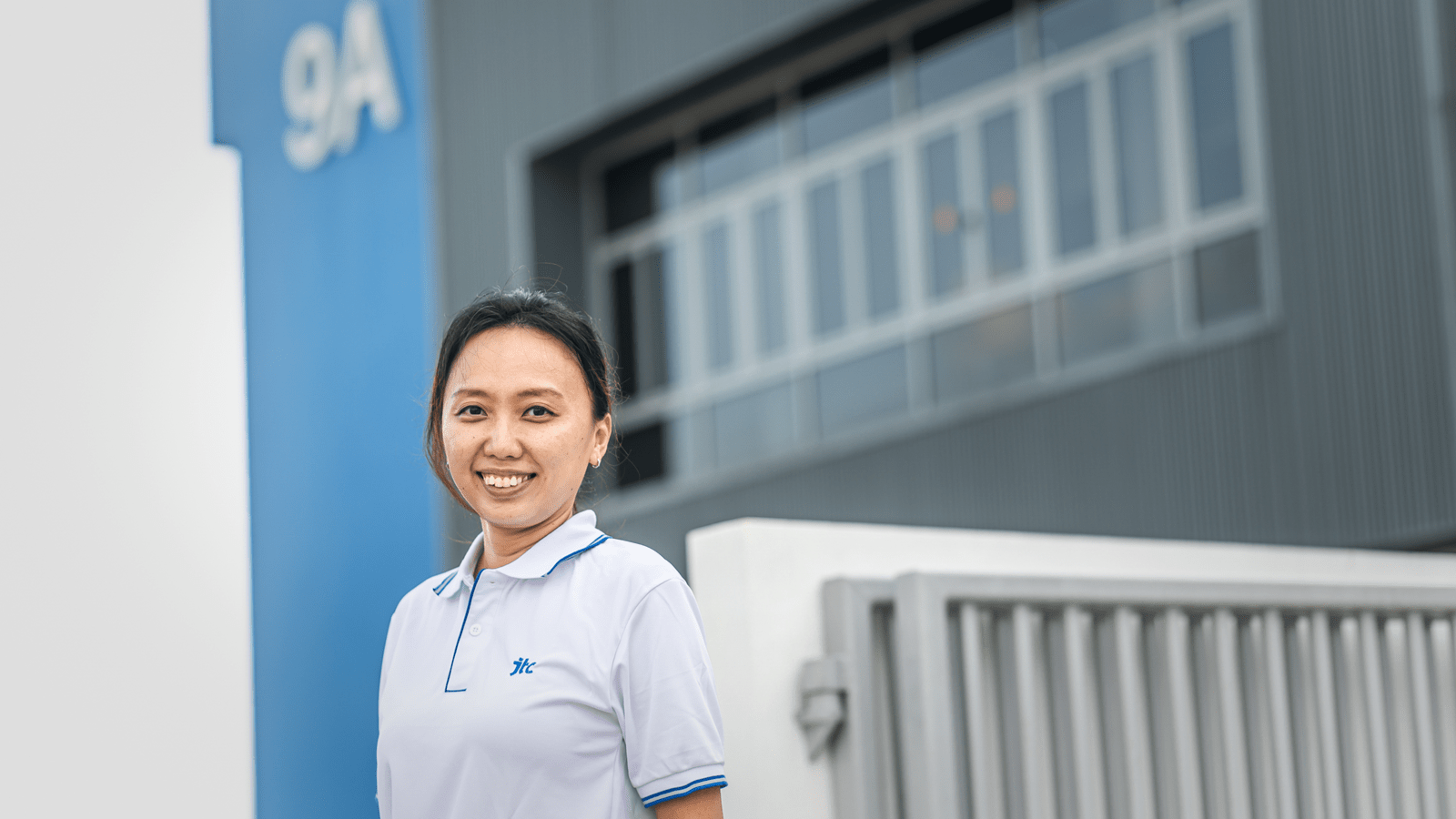
What are some benefits to adopting an in-house approach?
Teo: Firstly, an in-house team would inherently be more familiar with JTC’s standards and requirements. Thus, it was easier to manage expectations in terms of design, and there were less iterations and revisions needed. Furthermore, from the lessons gleaned from the earlier phases, we could take that into account and directly improve the design of the current phase of AS3. Secondly, it provides a platform for the team to hone our technical skill sets with on-the-job training.
Compared to the earlier phases, what is different about AS3’s design?
Zheng: Having overseen various industrial developments, we knew that every industry has its own unique requirements. When designing the buildings, we wanted to ensure that the specifications were tailored to suit the varying needs of the aerospace industry, be it for Maintenance, Repair and Overhaul (MRO) activities, or the manufacturing of aircraft engines and components.
As a result, the nine Standard Factory units in AS3 boast a mix of different sizes and heights to respond to the site context and companies’ business needs. Following engagement with the aerospace industry, we specifically finetuned our standard factory design to adopt smaller-sized modular units, with heavier floor loading and higher ceiling heights. The higher specifications help facilitate the introduction of Industry 4.0 activities as companies begin to deploy heavier equipment in their manufacturing process, as well as integrate automation and smart factory concepts.
Tan: Based on the learnings from the first two phases, we also adopted a more streamlined approach in design. The design of AS3 was standardised for all nine units in spatial layout, façade and roof profile, with improvements in design considerations such as removing walls between the office and production space to provide more flexibility, and a larger hoisting gate at the second storey to facilitate operations.
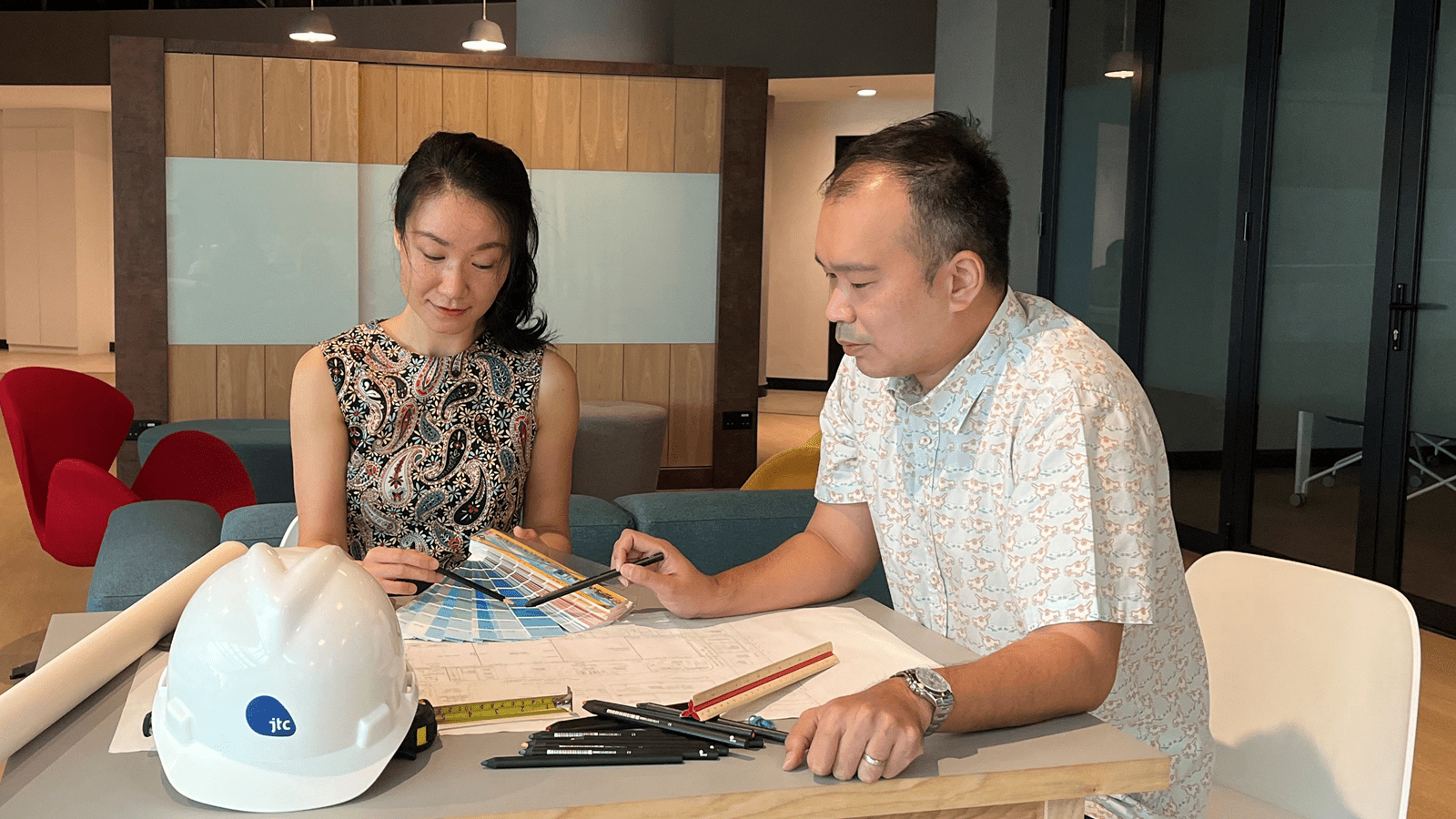
What were some challenges the team faced and how did you overcome them?
Zheng: Building close to an airport meant we had to be mindful about how high AS3 could go. Our teams were able to overcome this through careful design and planning and by adopting suitable construction materials and methods. For example, we have cast in-situ walls instead of precast panels for the façade and roof level to minimise the lifting activities required during construction that will exceed the height limit.
Teo: The site location posed a big challenge. Compared to the buildings from the other two phases, AS3 has the most stringent height constraints and lowest allowable buildable height. With the site being in the direct flight path of planes, we had limited time for piling works. We could only work at night due to high air traffic during the day. Moreover, in the event of an emergency landing, the team only had 10 to 15 minutes to bring down all the tall machinery. This required lots of close coordination and communication with the Seletar Airport control tower, especially during the piling and building phases.
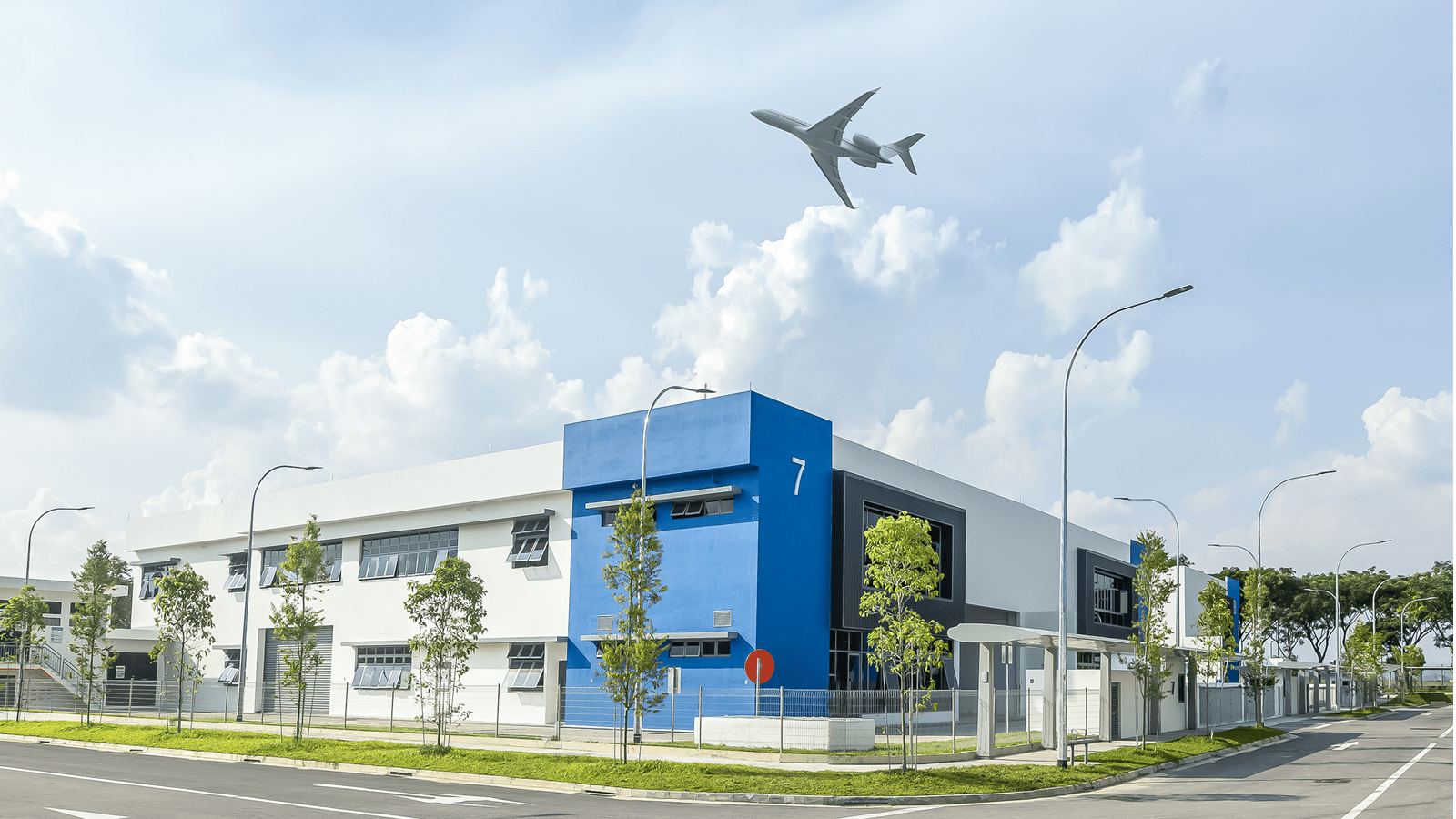
Also, since our buildings were cast in-situ instead of pre-casted, they were labour-intensive. This was exacerbated by the shortage of labour and sub-contractors pulling out due to financial difficulties, having been impacted by the pandemic. Work also had to be done on a very tight timeline too — we scheduled five completion dates and three TOP dates. I’m grateful that the team came together to make the project a successful one.
For this project, we adopted an Integrated Digital Delivery (IDD) approach from day one. This helped us to tide over many issues during the COVID period. For instance, since the design and subsequently the overall construction models were developed in Building Information Modeling (BIM), the team could continue collaborating during COVID through Virtual Design and Construction (VDC). We also deployed technologies such as 360° photos which enabled us to not only monitor matters such as site progress, safety and defects, but also allowed for prospective tenants to view the buildings when needed.
What were the most memorable moments for you?
Teo: Seeing everyone come together as a team was especially memorable for me. We even put in extra hours during the weekends to meet all the project deadlines and deliverables!
The team also went above and beyond to look out for each other when the going got tough. Unfortunately, the migrant workers working on the project were unable to return to their hometowns during the early stages of the pandemic, so we did whatever we could to provide moral support for them. After all, they are an integral part of our team ― nothing would have been possible without them.
Tan: The journey of working together as an in-house team with the contractors is a challenging but fulfilling one. In April this year, the team celebrated the project achieving TOP. We took in the view of the sunset on the rooftops of AS3 once again. This was a view we had enjoyed numerous times while the construction work was going on. This time however, there was a renewed sense of joy and confidence.
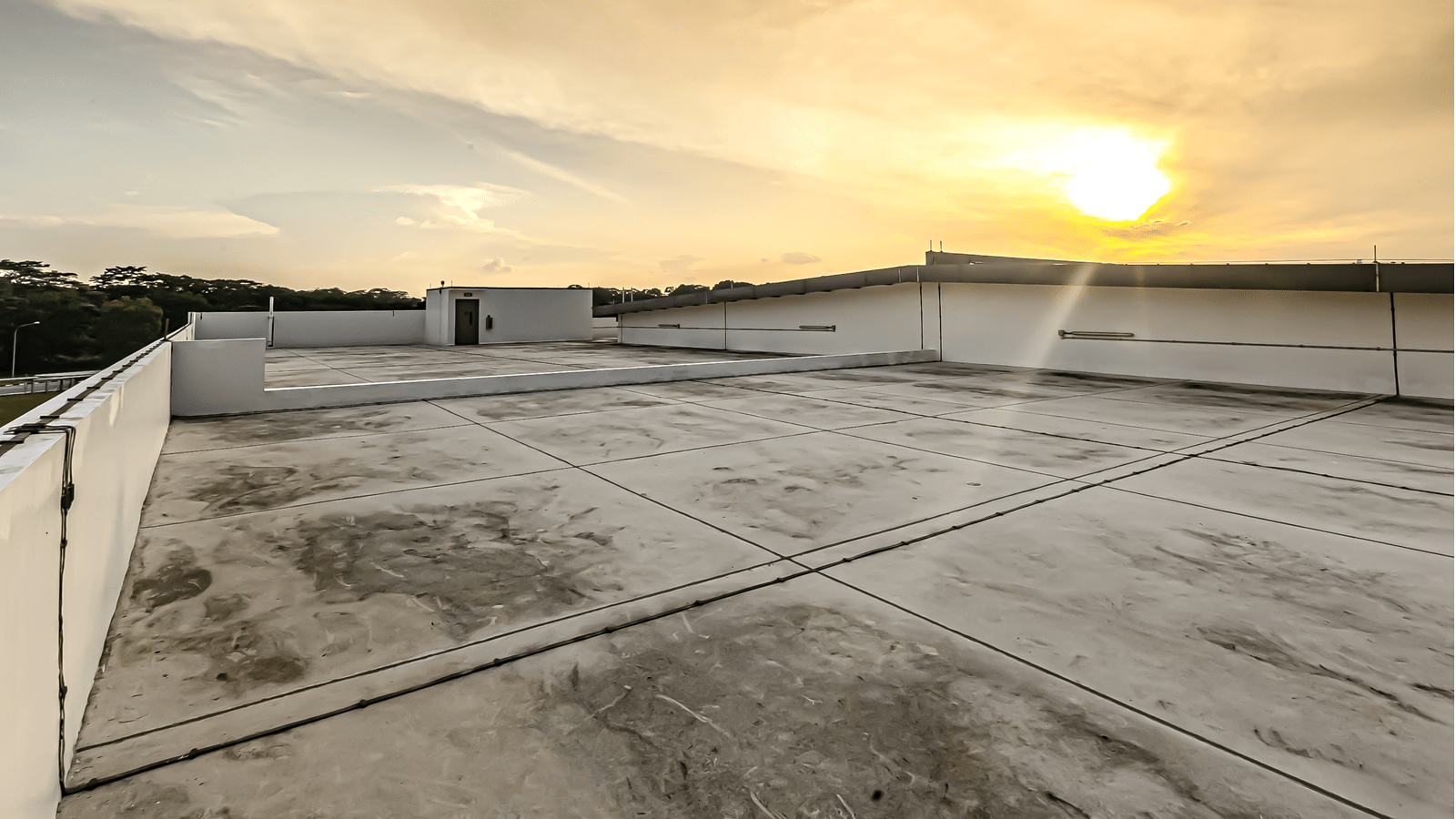